Pace of U.S. Hotel Development Is Being Threatened by Global Shipping Bottlenecks
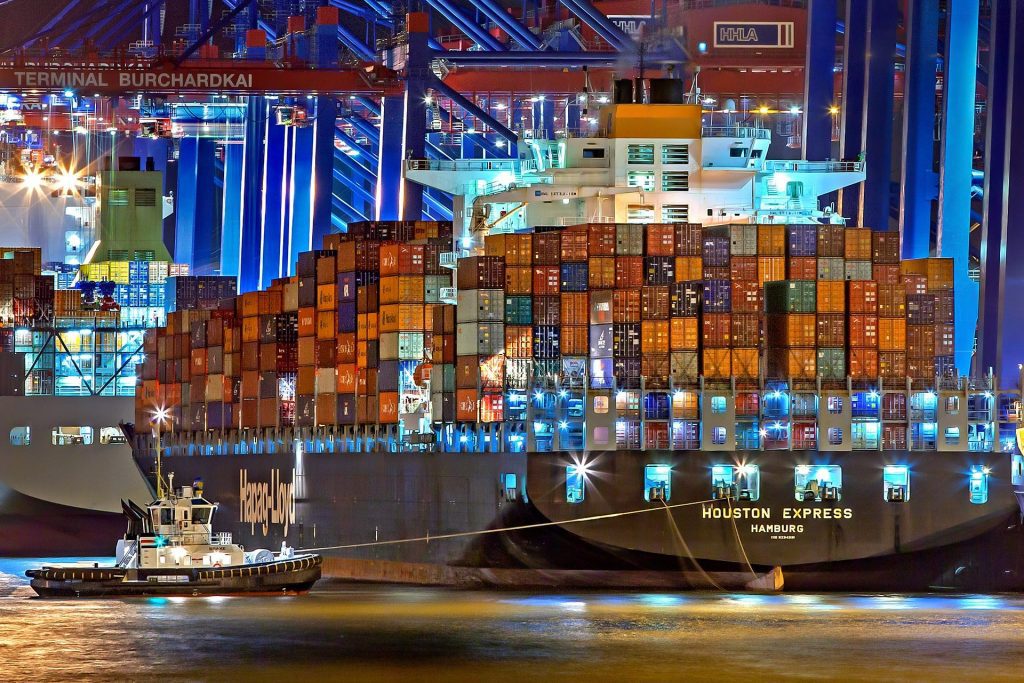
Skift Take
The surprising rise in consumer spending during the pandemic spurred a competition for goods and shipping containers among all industries. That's a long-term problem for hotels, especially with an expected increase in renovations around the corner that will require even more deliveries from overseas.
Rising lumber prices, manufacturing slowdowns, and a shortage of shipping containers is a perfect storm of issues threatening construction costs and timelines for U.S. hotel developers.
Random length lumber commodity costs were up nearly 271 percent from last year, just before the close of trading Thursday. Real estate developer Trinity Investments reports shipping container costs this week were up 614 percent from 18 months ago. Hotel furniture and equipment suppliers say there’s as much as an eight-week delay on upholstery and three months on larger goods.
None of these problems are expected to go away anytime soon, especially since there’s an expected wave of hotel renovations — put off during the pandemic — finally expected to take place across the U.S. over the next four years.
“If you're not prepared, and you're not planning for the disruption, you're going to get smoked right now,” said Joe Ward, vice president of asset management at Ohana Real Estate Investors, owner of properties like the Montage Beverly Hills.
Rising construction costs and labor shortages were already gripping the hotel industry before the pandemic, but supply chain issues around manufacturing and deliveries as well as the shipping slowdown are a newer frontier.
Many manufacturers quickly shut down production in the early weeks o